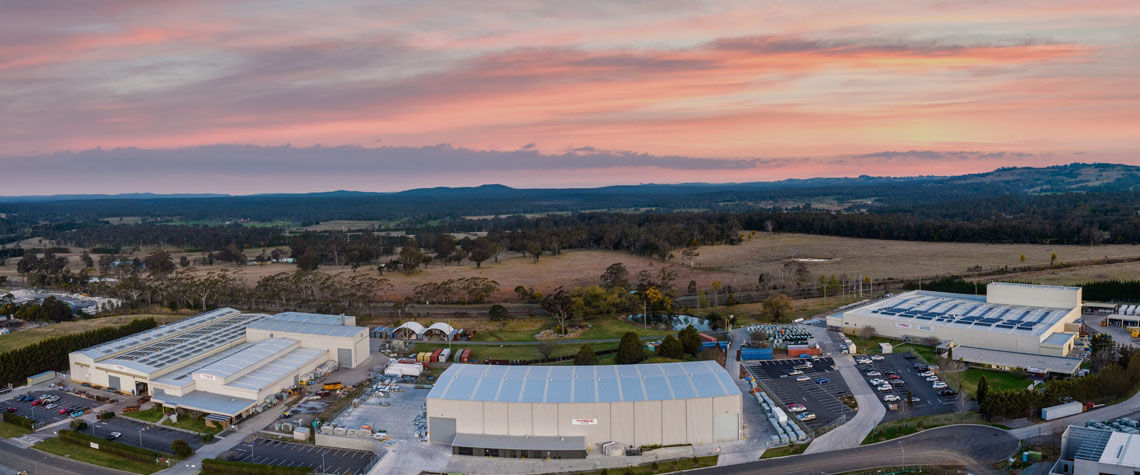
Located at Braemar near Mittagong in the attractive Southern Highlands of NSW with several fully serviced towns in the local area. Tyree’s operations are also located just 20 minutes from the expanding Wollondilly government area, a 30 minute drive from Campbelltown and 45 minute drive from the coastal locales of the Wollongong region. Tyree has continued to invest in our facilities by both upgrading existing workshops and constructing new buildings on the site to support the continued growth in products, expanding number of customers and an increasing market demand for our products.
Our business comprises three modern fully equipped workshops with over 20,000 square meters of floorspace on 30 acres of land owned by the company. The three workshops are dedicated to the following manufacturing activities: Pole Mount Transformer manufacture, Large Distribution Transformer manufacture, Power Transformer manufacture, Substation assembly and Metal Fabrication & Painting.
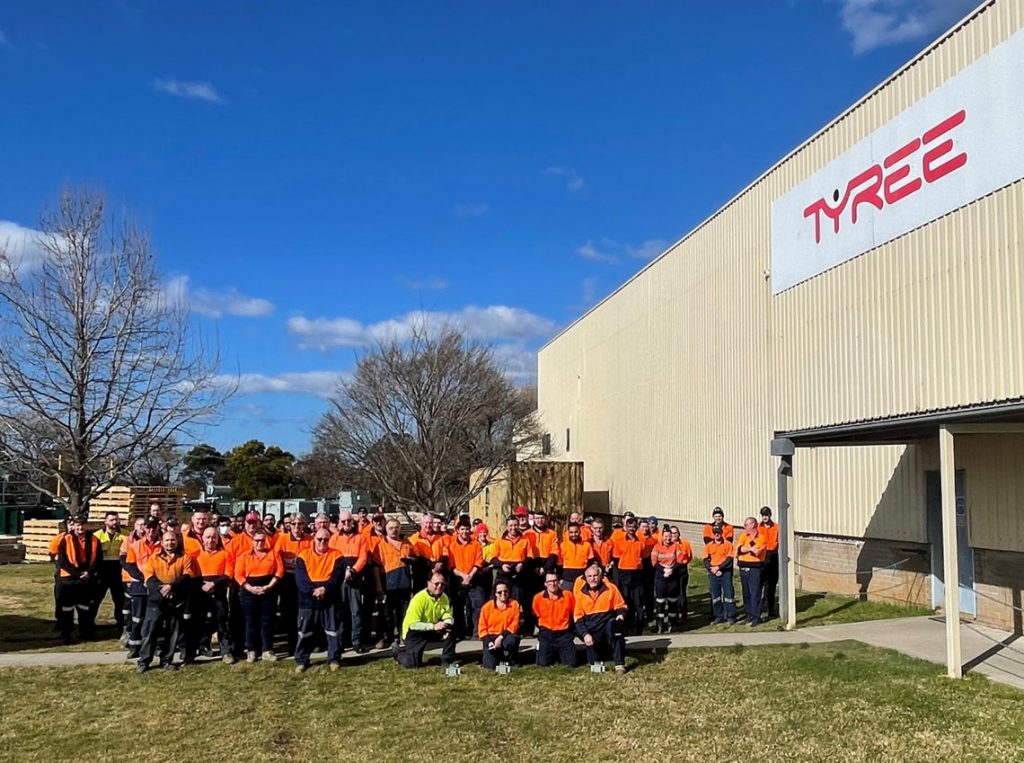
Tyree continually invests in the latest technology for manufacturing. Our capabilities include:
Steel and Sheetmetal Fabrication:
Located in a modern dedicated fabrication production workshop with overhead cranes and conveyorized material handling, our fabrication facility includes:
- Robotic welding – three GE FANUC Lincoln Electric robotic welding lines for high volume products
- CAD CAM Laser cutting for aluminium, stainless steel and mild steel – one of each Salvagnini 3kW and 6kW fibre laser with automated stacking tower
- Plasma cutting for heavy mild steel plate
- Pressing – three Salvagnini CNC Brake Presses
- Grit and shot blasting for surface preparation
- Painting lines – for both powder painting and spray painting
- Dedicated welding bays
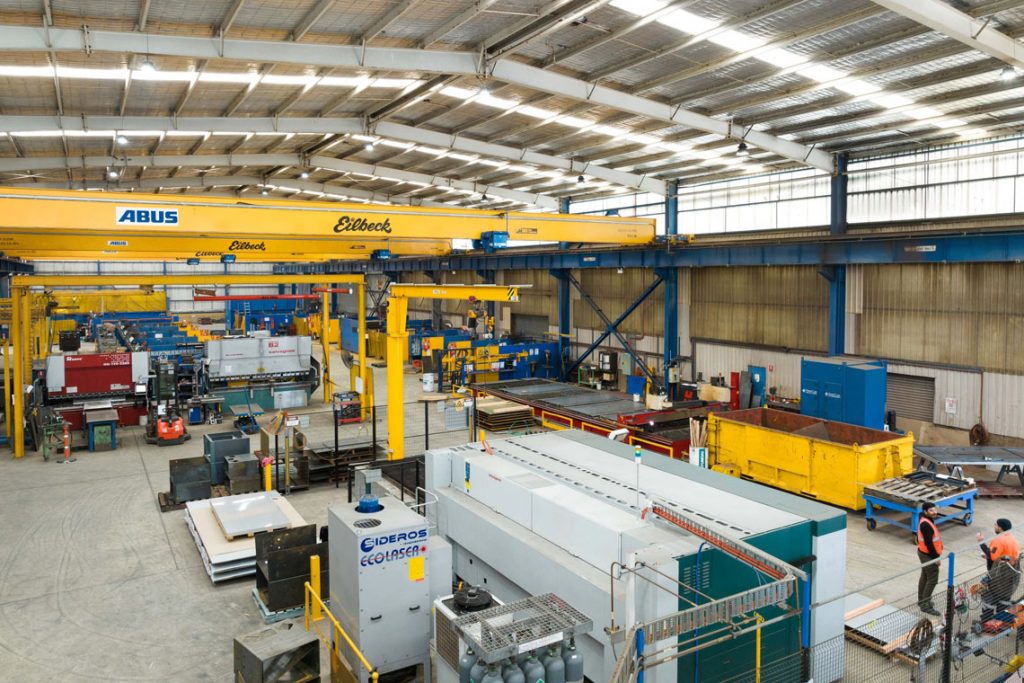
Transformer production:
Tyree’s three transformer production lines utilise the following world leading and modern equipment across our three production lines:
- AEM Unicore – Three semi-automatic machines and two fully automated machines for transformer core winding
- Steel slitting – automatic transformer core steel slitting line
- MTM Lamination line – automatic lamination cutting up to 650mm leg width
- HV Coil Winding – Three Tubaloy semi-automatic winding machines, seventeen manual coil winding machines
- LV Coil Winding – Two LAE semi-automatic foil winding machines with integrated welding, eight manual winding machines, two dedicated core annealing furnaces
- Insulation processing – paper slitting line, CNC router, automated spacer punch, insulation fabrication bay
- Transformer Drying – six vacuum drying ovens, two vacuum drying & filling chambers, three convection drying ovens
- Oil handling and processing – six hundred kilolitres of on-site oil storage, four oil filtration and treatment plants
- Power Transformer Test Bay – 1000kV Impulse Generator, Partial Discharge testing, 33kV supply for heat rise testing, sound level testing, SFRA, DIARANA, oil DGA and routine testing
- Distribution Transformer Test Bays – two dedicated test bays for routine testing of distribution transformers to 5MVA at 33kV
- Substation and LV Switchboard Test Bay – 300kV Impulse Generator, 80kV Hi-Pot, 400A Ductor testing, 5000A high current testing, 10kV Insulation testing
- Protection injection testing – Omicron three phase injection tests
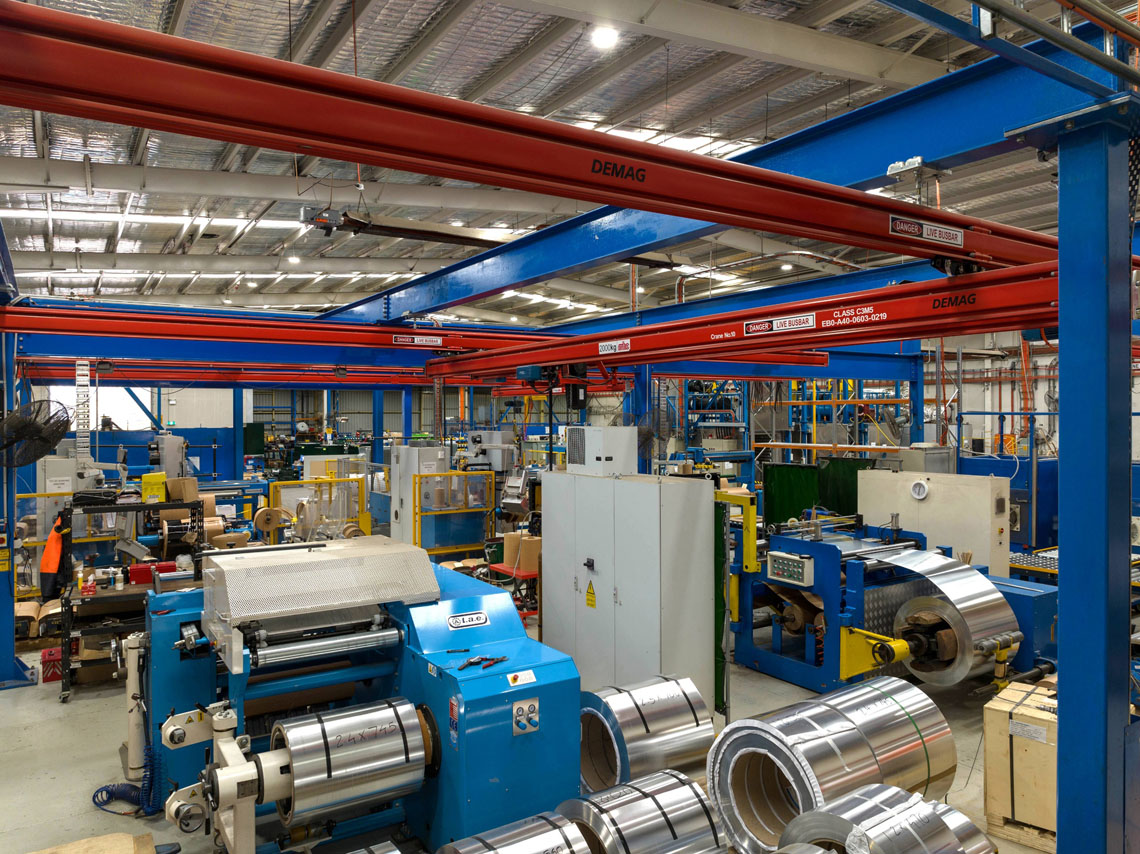
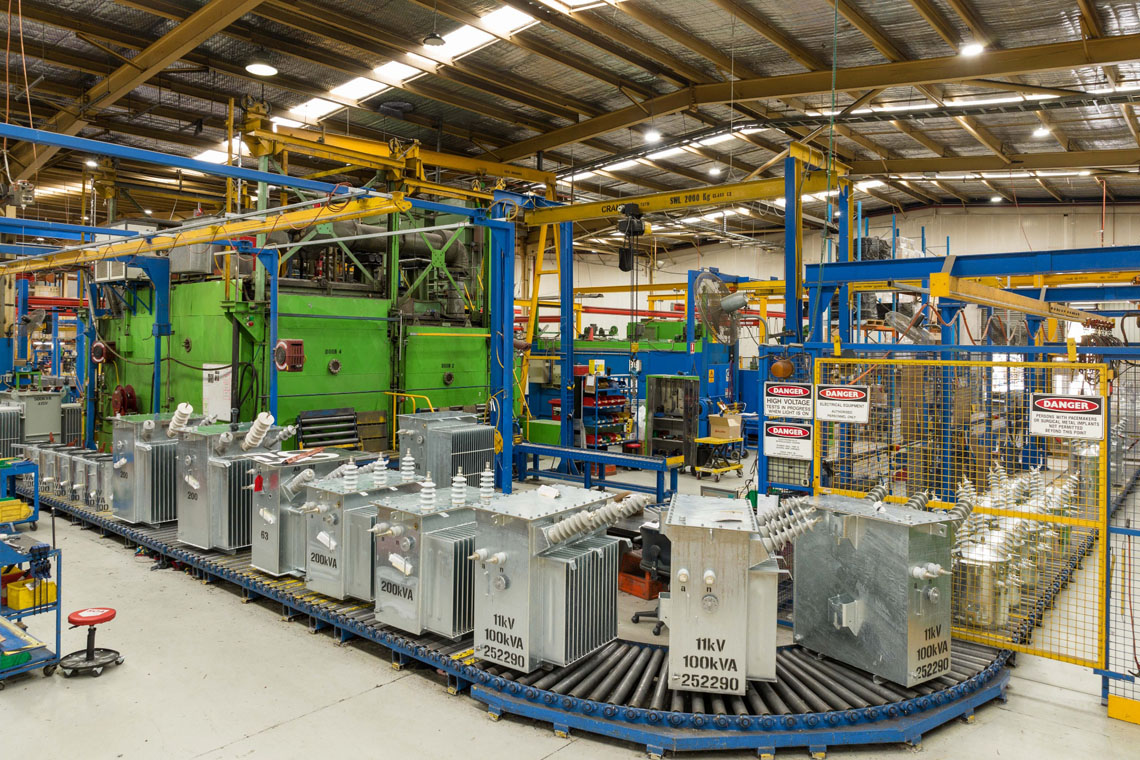
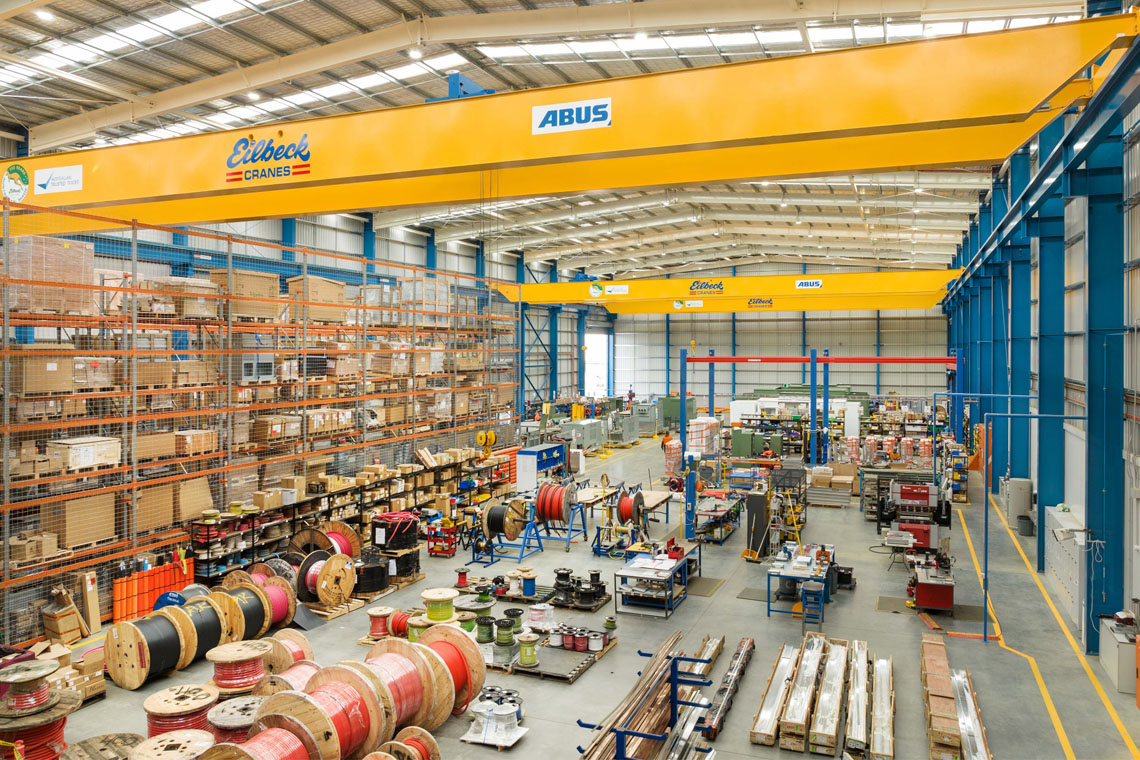
Engineering & Design:
Tyree utilises the latest software tools to in-house design our full range of products. The tools we use include:
- VIT SAPRTON – World leading transformer design software for power transformer design
- Solidworks – 3D modelling of products
- AutoCAD – Electrics software package for development of schematic and wiring diagrams
- Andersen software – for
- TySoft – Tyree in-house developed software for design optimisation of distribution transformers
Transport and Logistics:
Tyree provides transport and logistics support for our incoming raw materials used in production and delivery of our finished products to our customers throughout Australia, New Zealand and the Pacific region.
- 5,000 square metres of dedicated warehousing space for indoor storage of raw materials, components and sub-assemblies
- 15,000 square metres of dedicated secure hardstand for storage of finished transformers and substations
- 600 kilolitres of oil storage on-site
- Weighbridge for incoming and outgoing road transport
- Two modern prime movers and dedicated semi-trailers for product delivery and material movements
- Dedicated laydown area for devanning container freight and loading of outgoing shipping containers for export
- Fleet of twenty modern forklifts for loading and handling of raw materials and components